항만 탈탄소화
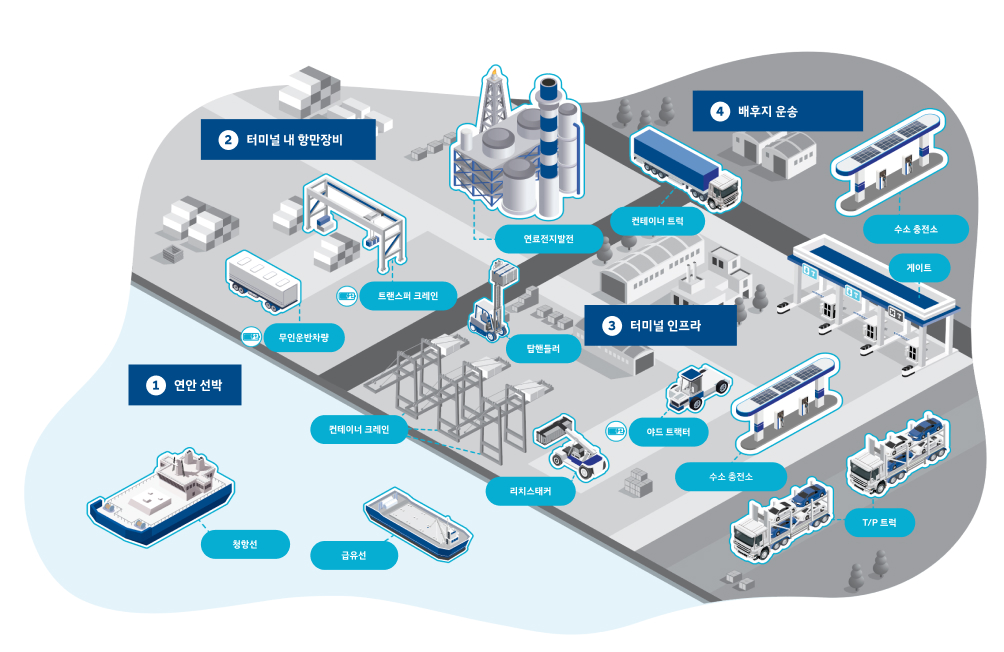
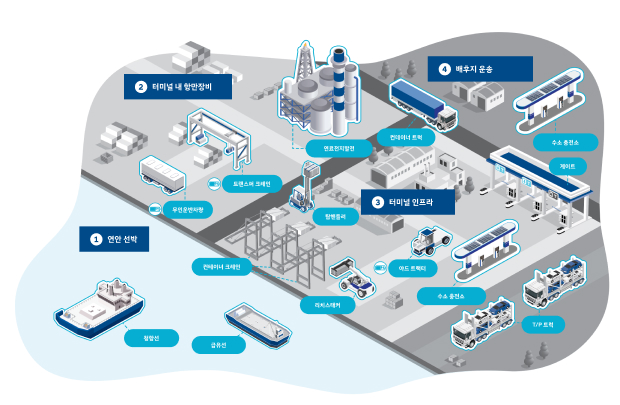
항만과 공항은 화석연료에 의존한 중장비 운영이 잦은 산업 허브로, 대기 오염이 심각한 곳입니다. 이러한 대기 오염을 완화시키기 위해 청정 수소에너지 기반 솔루션 제공이 효율적인 방안이 될 수 있습니다. 우선, 안정적인 수소 에너지 공급시스템을 구축하고, 화석연료에 의존하는 중장비들을 수소 연료전지 기반의 차량과 설비로 대체함으로써 물류 허브에서의 탄소 배출 감소에 기여할 수 있습니다.
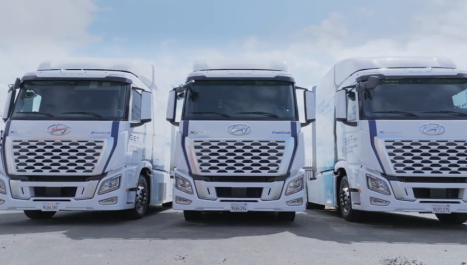
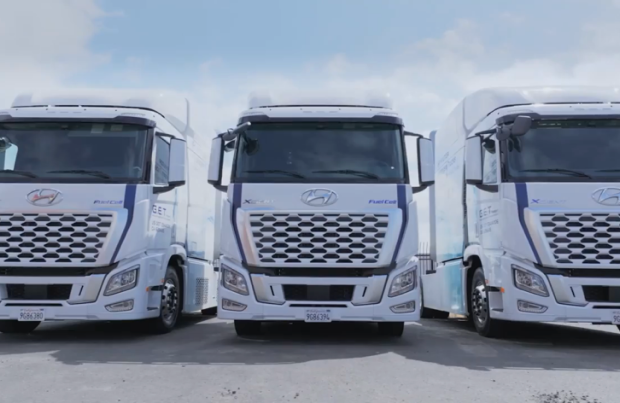
미국 캘리포니아 항만들은 수소 물류 허브로 개발되고 있으며, 정부 주도사업들을 통해 수소 에너지 시스템이 통합되고 있습니다. 현대자동차는 수소 연료전지 트럭 기반의 'NorCAL Zero-Emission'사업의 정식 공급업체로 선정되었으며, 이후 2023년 9월 오클랜드 항구에 30대의 엑시언트(XCIENT) 트럭을 성공적으로 공급했습니다. 이는 북미에서 가장 큰 규모의 대형 수소 연료전지 트럭 단일 배치 사업으로, 탄소 고배출 화물 트럭들을 대체하는데 기여했습니다.